Creating a new environmentally friendly industry: Green ceramics will become a future development trend
Release time:
2019-01-22
Under the increasingly severe threats of ecological and climate problems, people's environmental awareness has gradually increased, and many industries are experiencing a wave of low-carbon, environmentally friendly, and energy-saving practices. The ceramics industry is no exception.
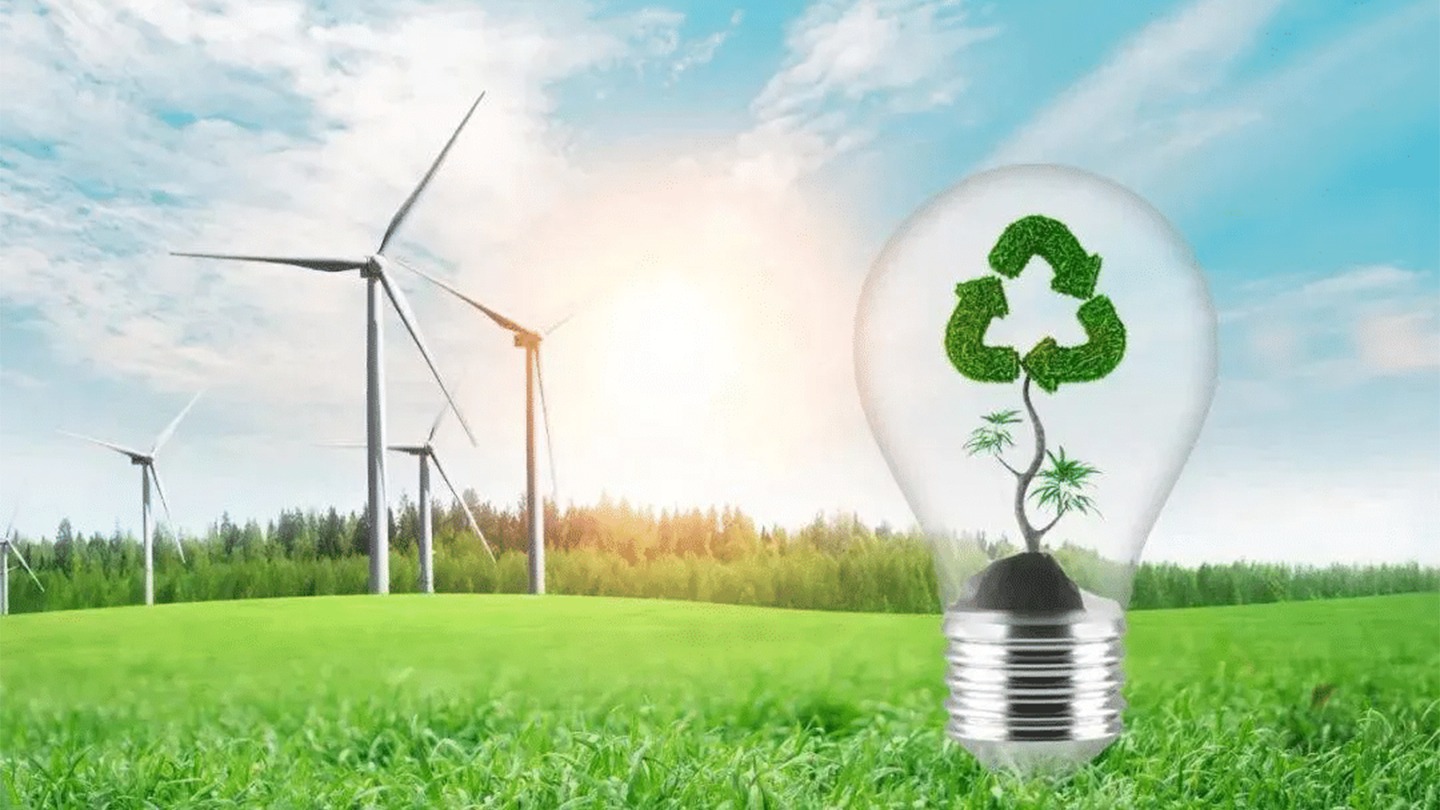
Under the current severe threats of ecological and climate issues, people's environmental awareness has gradually increased, and many industries are experiencing a wave of low-carbon, environmentally friendly, and energy-saving practices. The ceramics industry is no exception.
I. Green Ceramics: The Current Development Trend in the Ceramics Industry
The ceramics industry is currently developing towards green (environmentally friendly) ceramics that benefit human civilization and health. The standards for green ceramics are:
1. Conserve energy and raw materials, and make full use of resources.
2. Minimize the emission of environmentally polluting waste gases (SO2, CO, CO2, NOx, and smoke dust, etc.).
3. Minimize the discharge of wastewater harmful to humans (containing lead, cadmium, mercury, chromium, and other heavy metal elements).
4. Absence of radioactive substances harmful to human health.
5. Promote the production of ceramics with health-enhancing functions such as self-cleaning, antibacterial, and sterilization.
6. Minimize dust and free silica.
7. Minimize noise and heat loss.
8. Maintain a clean, hygienic, and comfortable production and work environment.
II. Methods for Reducing Energy Consumption in the Ceramics Industry
1. Develop green kilns.
China is a country with relatively scarce energy resources, and the ceramics industry is a major energy consumer. In the future, the development direction of Foshan ceramic kilns will shift from the past proposals of roller kilns, gasification, lightweight, automation, and large-scale to green (environmentally friendly, energy-saving, and intelligent) kilns.
Efforts to achieve green kilns include: reducing the electro-mechanical consumption and noise of kilns; researching advanced energy-saving and low-pollution burners; using new refractory materials and coatings; researching new intelligent automatic control methods; and establishing a waste gas purification research and testing center.
Achieving Green Kilns
Recently, the Guaneng ball mill dedicated controller developed by Foshan Guanling Automation Technology Co., Ltd. features a unique automatic energy-saving function, achieving energy savings of more than 15%. If the ball mill hydraulic coupler is removed, the energy saving rate will reach more than 20%. After installation, the ball mill starts with soft start, greatly reducing the impact force on the ball mill, extending the lifespan of the ball mill belt, shaft, gearbox, and gears. After installation, the starting current of the ball mill can be controlled below 1.2 times the rated current. (According to actual measurements, the current of a typical imported soft starter when starting a ball mill is about 4 times the rated current) Therefore, the soft start performance of this controller is excellent. Due to the low starting current of the ball mill, it will not cause grid fluctuations and voltage drops, eliminating other power equipment tripping and malfunction phenomena caused by this. It has complete overload, overcurrent, short-circuit, and grounding protection functions. It also allows easy setting of grinding time and automatic shutdown time, and easy selection of additional grinding time. It has a high return on investment, with all investments recoverable through electricity savings in about 5-8 months. It is currently in use at Xinmingzhu and Shenghua ceramic factories, achieving good results.
Domestic slurry preparation uses batch ball mills, while developed countries generally use continuous ball mills, increasing output by more than three times and reducing power consumption by more than three times. The feeding and discharging during ball milling are fully automated, eliminating the need for shutdown, facilitating the production of concentrated slurry, and allowing subsequent spray dryers to save energy by 10%-35%.
4. Large spray drying towers
Large spray drying towers save energy per unit of electricity; for example, the 7000 type saves about 10% more energy than the 3200 type.
5. Intermittent stirring of slurry tanks
A time relay is installed on the slurry tank motor, stirring for 20-30 minutes and stopping for 30-40 minutes, preventing the slurry from settling and saving more than 50% of electricity.
6. Using large-tonnage brick presses and new air compressors
Large-tonnage brick presses exert high pressure, resulting in high-quality, high-yield brick blanks with high qualification rates and specialized energy-saving designs, saving 20%-27% of electricity.
Using new single-screw air compressors instead of old air compressors can save more than 30% of electricity and significantly reduce noise.
7. Single-firing technology
Single firing saves a significant amount of energy compared to double firing. 90% of floor tiles and exterior wall tiles in China use single firing. Only 10% of interior wall glazed tiles use single firing. Efforts should be made to research the composition of the body and glaze suitable for single-firing interior wall glazed tiles to increase the proportion of single firing, saving more than 30% of energy and electricity consumption.
8. Low-temperature rapid firing
Increasing flux components, selecting raw materials suitable for rapid firing (such as wollastonite and diopside), and using appropriate kilns (such as roller kilns). Achieving low-temperature rapid firing is an effective way to save energy in firing. For example, if the firing temperature is reduced from 12800C to 11800C, the firing energy consumption can be reduced by 30%.
9. Selecting kiln body materials and coatings with good thermal insulation performance
Using small-capacity, high-temperature resistant ceramic fibers as kiln body insulation materials can reduce the external temperature of the kiln to around 500°C, reducing heat loss. The goal is to further reduce fuel consumption by 10%-20%, increase thermal efficiency by 10%-20%, reduce electricity consumption by 10%-30%, significantly reduce noise and dust, and bring China's ceramic kilns to the world's advanced level.
2. Gap between China's energy consumption level in building sanitary ceramics and that of advanced international levels
Over the past two decades, the development of ceramic kilns in China has gone from down-draft kilns to muffle tunnel kilns and then to roller kilns, and the fuel has gone from coal to oil and then to gas, resulting in a significant reduction in energy consumption. Kiln energy consumption has dropped from 40%-45% of production costs in the early 1980s to 30%-35% today. However, there is still a considerable gap compared with the international advanced level. The main energy consumption indicators are shown in Table 1.
Using high-temperature resistant far-infrared coatings on the kiln inner walls can increase radiative heat transfer and save 5%-8% of energy.
10. Using lightweight, low-heat storage kiln cars
The heat retention of kiln cars when they leave the tunnel kiln is considered a heat loss, so lightweight materials should be used extensively to reduce the heat retention of the kiln cars. The latest lightweight kiln cars are filled with ceramic fiber inside high-alumina mullite and cordierite plates. They possess the stability and performance of traditional kiln car materials, but their heat retention is reduced by 70%, significantly reducing fuel consumption and maintenance costs.
11. High-speed energy-saving nozzles
High-speed energy-saving burners generate strong heat and airflow inside the kiln, improving heat transfer and leading to widespread adoption. Compared to traditional burners, these burners can save 10%-15% fuel.
12. Waste heat recovery
The waste heat from the cooling zones of tunnel kilns and roller kilns can be used for semi-finished product drying and auxiliary combustion air preheating. The higher the preheating temperature, the more fuel is saved. Preheating the combustion air to 400°C saves 17% more fuel than preheating to 150°C, and preheating to 600°C saves 28%.
Waste gas from tunnel kilns and roller kilns can be recovered through waste heat boilers and heat pipe heat exchangers, or used to dry semi-finished products.
13. Automatic control
Using intelligent computer-based automatic control for kilns stabilizes temperature, atmosphere, and pressure, improving product quality and saving 5%-10% energy.
14. Super energy-saving scraping and rough polishing machine
Foshan Nanhai Kote Electromechanical Co., Ltd.'s new energy-saving scraping and rough polishing machine is a new machine type with scraping and rough polishing functions. It can create a smoother, more even surface and consistent thickness for ceramic tiles, significantly improving polishing output, quality, and gloss. It is innovative not only in structure but also in its process, achieving an innovative breakthrough by replacing grinding with scraping. It can save the company 170,000 yuan in energy consumption per month and truly achieve one machine per kiln, reducing the cost of polished tiles by about 30%.
15. Using variable frequency drives
For fans above 10 kW, the drive system, oil pump, and installation of variable frequency drives in roller kilns can save 10%-30% electricity.
16. Reducing fan power consumption and noise
Currently, advanced foreign fans have noise levels of 50-70 decibels, which is relatively low. Domestic fans have noise levels of 80-90 decibels, some even exceeding 100 decibels, which is very loud.
Foreign kilns use fans with a power of 70-90 kW, while domestic fans use 130-170 kW (calculated based on building sanitary ware kilns with the same output).
The core technology for reducing fan power consumption lies in the selection of fan blade materials. Imported fan blades use high-strength aluminum alloy with a specific gravity of 2.5-2.7 tons/m3, while domestic fan blades use manganese steel with a specific gravity of 7.8 tons/m3. If domestic fan blades use heat-resistant aluminum alloy and are redesigned and improved, and the assembly quality is improved, then the power consumption and noise of domestic fans could approach and reach the level of imported fans. If each kiln saves 50 kW, the annual electricity saving is 400,000 kWh. Based on 10,000 kilns in the national ceramics industry, this could save 2 billion kWh annually and significantly reduce noise in the firing workshop.
III. Recycling and Application of Waste and Low-Quality Materials
1. Wastewater from production, after treatment by water treatment equipment, has harmful substances removed and is filtered before being reused in production.
2. The fine powder from the spray tower dust collector is directly sent to the slurry pool, mixed into slurry, and then mixed in the transfer slurry tank before being sent to the spray tower for material making.
3. After selecting and cleaning defective sanitary ware semi-finished products, they are ground into slurry in a ball mill (they can be ground separately or 5%-10% can be added to the ball mill each time).
4. Defective sanitary ware products, after cleaning and crushing into mature materials, are added to the ball mill as aggregates, reducing shrinkage, deformation, cracking, and pinhole defects. When added to the glaze, it improves the gloss of the sanitary ware glaze.
5. Defective wall and floor tile semi-finished products, after classification and cleaning, can be reused in the ball mill as colorants and body materials (such as crystal tiles, antique tiles, etc.).
6. After cleaning and breaking into appropriate sizes, defective wall and floor tile products can be put into the ball mill as ball pebbles without affecting product quality.
7. Ceramic waste materials can be used to develop solid concrete, non-fired square tiles, and road tiles.
8. Ceramic waste materials can be used to develop wall and floor tiles, filters, etc.
9. Using smelting furnace waste slag as the main raw material to produce unique hard-as-diamond, jade-like green building materials, metal tiles. Red, white, and gray metal tiles can also be produced, and some can also be used to produce colored glazes.
10. Using iron oxide-containing minerals to replace titanium dioxide (titanium white) to produce gold-flowered beige products. Calcined kaolin (3000 yuan/ton) can also be used to replace titanium dioxide (about 9000 yuan/ton) to produce gold-flowered beige products.
11. Worn ceramic plungers of double-cylinder slurry pumps, after being ground and processed (a few millimeters), can be reused with wear-resistant rubber rings, with repair costs only 1/3 of the original price.
12. Used machine oil from grinders and other equipment in the ceramic machinery industry, and hydraulic oil from automatic brick presses, after treatment and filtration, can be reused, saving 50% of the cost.
13. We should gradually investigate and clarify the current status of raw materials in China's ceramic industry (including high and low temperatures and quality), formulate a long-term, reasonable, and scientific development and utilization plan, and improve the standardized production of raw materials to prevent resource waste and low efficiency (high-grade raw materials should produce high-grade products, and medium and low-grade raw materials should also strive to produce good products).
14. After processing, ceramic waste and defective products (over 13 million tons annually nationwide) can be used, saving a large amount of valuable land resources needed for landfill, benefiting future generations.
15. Daring to use red blanks and other low-quality materials for ceramic blanks can greatly broaden the development prospects of the ceramics industry.
16. The realization of the recycling of waste and low-quality materials in the ceramics industry will enable China's ceramics industry to keep pace with the times, opening up a bright path for its long-term, healthy, and sustainable development in the future.
17. By improving the sealing treatment of ceramic raw materials during transportation, storage, and production, it is possible to greatly reduce the dust flying in the environment and create a clean environment with clear water and blue sky.
Through the above measures, the damage of the ceramics industry to the environment can be greatly reduced, and a new industry has been created while protecting the environment.
3. Ball milling process
The power consumption of ball milling slurry accounts for 60% of the total power consumption of a ceramic factory. By adopting a reasonable ratio of materials to balls, selecting efficient water reducers, grinding aids, and alumina linings, alumina balls can improve grinding efficiency and shorten the ball milling cycle. Selecting large-tonnage ball mills can reduce power consumption by 10%-30%. Increasing the concentration of the spray drying tower slurry can significantly reduce the heat consumption of the spray drying tower. If the concentration of the spray drying tower slurry is increased from 60% to 65%, the unit heat consumption can be saved by 21%, and if the concentration is increased from 60% to 68%, the energy consumption can be saved by 33%. This can be achieved by adding efficient reducing agents.
Tag:
Contact Us
Tel: 86-0713-8663193
Yu Yuanlin: 86-13871998019
Hong Hui: 86-13907259535
Yu Shiyun: 86-17798384875
E-mail:zhongaokiln@163.com
Address: Building A3, Guanggu United Science and Technology City, Huangzhou District, Huanggang City, Hubei Province